Ford zamierza poprawić do perfekcji jakość spasowania nadwozia produkowanych samochodów. W tym celu zaadaptował do pracy specjalny skaner 3D, błyskawicznie kontrolujący jakość produkowanych części i ich montażu.
Ford Motor Company przekonuje, że wykorzystuje najnowocześniejsze technologie, aby zagwarantować najwyższą jakość swoich pojazdów oraz precyzję w produkcji części i paneli nadwozia na poziomie 99,99 procent. W tym celu używa najnowocześniejszych urządzeń, w tym skanera 3D. I choć te zapewnienia można podważyć, patrząc na jakość spasowania nowych Fordów, to amerykański koncern zapewnia, że nowy Ranger, dzięki temu skanerowi, wprowadzi markę na nowy poziom jakościowy.
Skaner 3D kontroluje jakość części i ich spasowanie
Panele samochodu są skanowane przy użyciu skanera 3D ScanBox, którego efektywność przewyższa tradycyjne metody pomiarowe o nawet 80 procent. To urządzenie jest zdolne do kompleksowego skanowania, inspekcji i raportowania za naciśnięciem jednego przycisku. Andrew Fromholtz, główny inżynier ds. nadwozi i tłoczenia w Ford International Markets Group (IMG), podkreśla, że skaner strukturalny ScanBox z niebieskim światłem zapewnia, że każdy pojazd Forda produkowany w zakładach Ford Thailand Manufacturing (FTM) lub Silverton w RPA spełnia rygorystyczne standardy jakości.
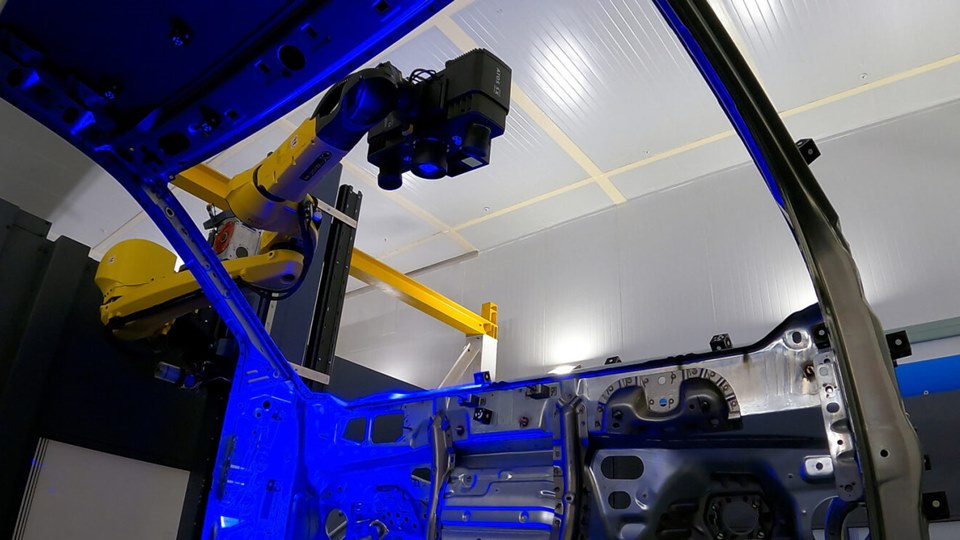
Zobacz: Jak usunąć rdzę z tylnego błotnika? Naprawa krok po kroku!
W Silverton w RPA Jan Groenewald zarządza tłocznią, w której produkowane są panele nadwozia nowego Forda Rangera. Groenewald wyjaśnia, że celem jest osiągnięcie dokładności na poziomie 99,99 procent we wszystkich częściach nowego Rangera, a narzędzia takie jak skaner strukturalny niebieskiego światła są kluczowe do osiągnięcia tego celu.
Skanowanie tańsze, lepsze i szybsze
Proces działania systemu ScanBox polega na skanowaniu rzeczywistej części i porównywaniu jej z modelami 3D opracowanymi komputerowo (CAD), co ma gwarantować idealne dopasowanie. Skaner nie tylko mierzy wymiary obwodowe części, ale także parametry jej powierzchni. I co najważniejsze dla producent, robi to szybko i precyzyjnie. Technologia skanowania strukturalnego z użyciem niebieskiego światła okazuje się bardziej ekonomiczna i efektywna niż tradycyjna metoda maszynowego pomiaru współrzędnych (CMM). Skanowanie obiektów zajmuje zaledwie kilka sekund, a wyniki mogą być przekształcane w bardziej użyteczne informacje zwrotne dla techników.
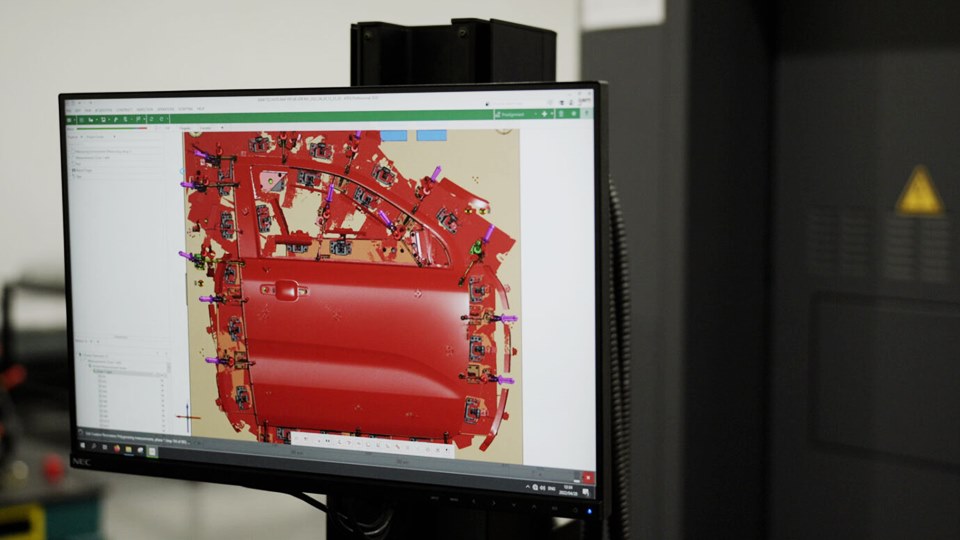
Groenewald podkreśla, że dzięki temu systemowi możliwy jest pomiar części w zaledwie dwie minuty i 50 sekund, w przeciwieństwie do godziny do półtorej wymaganej przy użyciu tradycyjnych metod CMM do pomiaru dachu. To oznacza, że części mogą szybciej trafiać do produkcji, a wszelkie usterki są wykrywane i usuwane na wczesnym etapie. Rangery produkowane w RPA i Tajlandii są eksportowane do ponad 180 krajów.
Zobacz: Regeneracja samochodu? Stellantis odnawia auta i wprowadza znowu na rynek!
Dodaj komentarz