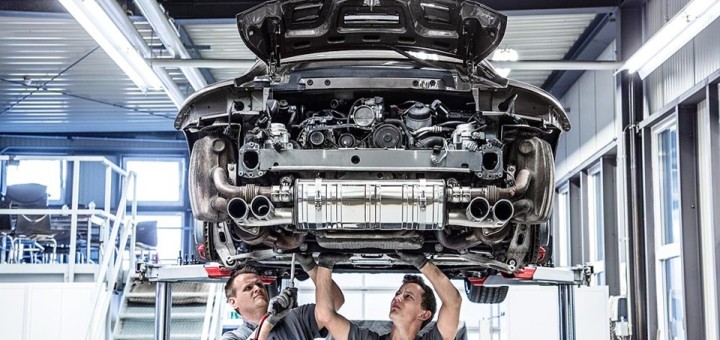
Brak części zamiennych spowodowany zakończeniem produkcji auta to problem, z którym często borykają się właściciele zarówno samochodów zabytkowych, jak i młodszych youngtimerów. Kłopot ten jest szczególnie widoczny w przypadku limitowanych, sportowych modeli samochodów. Firma Porsche znalazła rozwiązanie tego problemu. Jest nim drukowanie części w 3D!
Jeśli jesteś właścicielem np. Audi V8, Mazdy Xedos 9 czy Mitsubishi CZT to dobrze wiesz, że niektóre części do tych aut są albo trudno, albo już w ogóle niedostępne w sprzedaży. Ale jeszcze większe problemy dotyczą samochodowych ikon takich które były produkowane w naprawdę niewielkich seriach. Supersportowe Porsche lat 80-tych czyli model 959 powstało w zaledwie 292 egzemplarzach. Tak mała seria sprawia, że wytwarzanie małych partii podzespołów za pomocą specjalnie opracowanych na ich potrzeby narzędzi, byłoby w dużej mierze nieefektywne. Dość dokładnie opisują to przedstawiciele Porsche.
Części zamienne do starszych modeli Porsche
Oferta Porsche Classic obejmuje na dzień dzisiejszy około 52 tysięcy części. Jeśli danego elementu nie ma już w magazynie lub jeżeli zapasy magazynowe są niewielkie, jest on wytwarzany przy użyciu oryginalnych narzędzi. Jeśli zapotrzebowanie na dany podzespół jest duże, to dopuszczalnym jest, aby w jego produkcji zastosować nowy sprzęt (narzędzia). Jednak problem pojawia się w przypadku wspomnianych, niskoseryjnych samochodów. To poważne wyzwanie gdyż wytwarzanie małych partii części za pomocą opracowanych specjalnie na ich potrzeby nowych narzędzi byłoby w dużej mierze nieopłacalne. I właśnie dlatego Porsche coraz śmielej używa do takich rozwiązań drukarek 3D.
Części zamiennie z drukarki 3D – na czym to polega?
Proces produkcji części zamiennych z wykorzystaniem drukarki 3D prześledzimy na przykładzie unikatowego Porsche 959. Załóżmy, że z oferty ASO zniknęły widełki sprzęgła do tego modelu. Z jednej strony ten wykonany z żeliwa szarego element podlega bardzo surowym wymogom jakościowym, z drugiej – klienci zamawiają go niezwykle rzadko, choćby z uwagi na fakt, że supersportowy model jest niesamowicie rzadkim autem. Jedynym wartym rozważenia procesem produkcyjnym jest tu selektywne topienie laserem (SLM). Żeby wyprodukować wspominanie widełki sprzęgła, w ramach skomputeryzowanego procesu na płytkę bazową nakłada się warstwę sproszkowanej stali narzędziowej o grubości mniejszej niż 0,1 mm. Następnie w obojętnej atmosferze wiązka światła laserowego topi proszek w określonych miejscach, tworząc stalową warstwę. I dokładnie w taki oto sposób, warstwa po warstwie, powstaje trójwymiarowy element.
Co niezwykle ważne, „wydrukowane” widełki sprzęgła bez żadnych problemów zaliczają zarówno próbę nacisku z obciążeniem niemal 3 ton, jak i późniejsze badanie tomograficzne pod kątem wewnętrznych usterek. Nienaganną jakość oraz funkcjonalność komponentu potwierdzają praktyczne testy dźwigni zamontowanej w pojeździe testowym i szeroko zakrojone testy drogowe.
Drukarka SLS
Bardzo pozytywne wyniki tego typu produkcji części sprawiły, że Porsche wykorzystuje obecnie druk 3D do produkcji ośmiu innych elementów. Części te są wykonywane ze stali i stopów w procesach selektywnego topienia laserowego, a także z tworzyw sztucznych, przy użyciu drukarki SLS. Za skrótowcem „SLS” kryje się selektywne spiekanie laserem – proces, w którym zbiornik podgrzewany jest do temperatury tuż poniżej temperatury topnienia, a plastikowy proszek zostaje w wybranych punktach utwardzony (spieczony) promieniem lasera.
Jakość i trwałość części samochodowych z drukarki 3D SLS
Zdaniem inżynierów Porsche, wszystkie elementy podlegają przynajmniej tym samym wymogom jakościowym, jak te stosowane w pierwotnym okresie produkcji, ale zwykle spełniają jeszcze wyższe standardy. Dokładność rozmiaru i dopasowania zapewniają testy zamontowanej już części. Zależnie od obszaru zastosowania, elementy plastikowe wytwarza się z różnych materiałów, które – tak samo jak oryginalne części – muszą być odporne na działanie olejów, paliw, kwasów i światła.
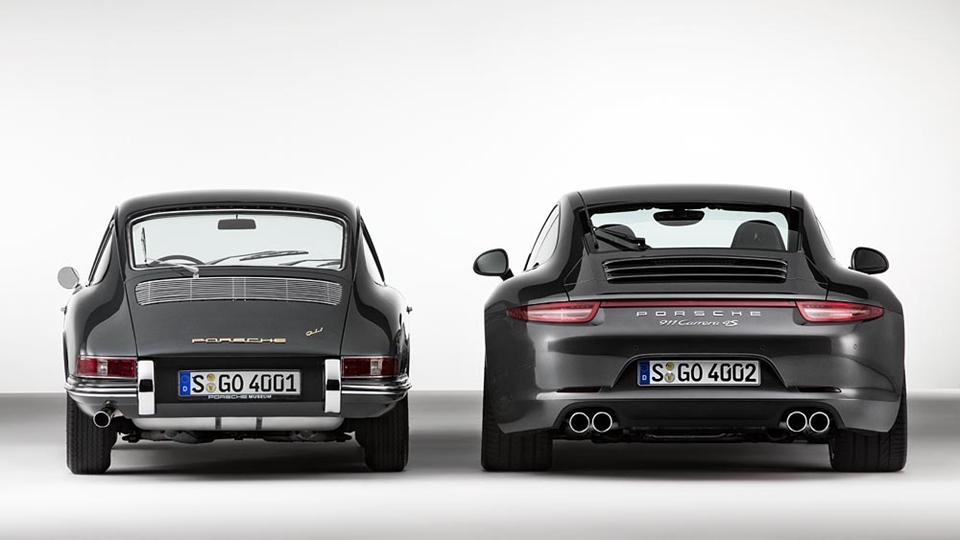
Niezależnie od wieku auta, Porsche chce zapewnić mu dostęp do oryginalnych części. Teraz także z drukarki 3D!
Na dzień dzisiejszy, Porsche Classic poddaje analizie, czy wydruk 3D będzie właściwym rozwiązaniem do produkcji 20 kolejnych elementów. Wśród największych korzyści wymienia się dwie rzeczy. Po pierwsze, aby rozpocząć produkcję wystarczą trójwymiarowe dane projektowe lub trójwymiarowy skan podzespołu. Po drugie, części mogą być wytwarzane zgodnie z realnym zapotrzebowaniem występującym na daną chwilę, a to eliminuje koszty narzędzi oraz przechowywania komponentów.
Na drukarce 3d to i podobno elementy domu czy protezy można wydrukować także przyszłościowe narzędzie ale koszty są ogromne póki co, no i sie trzeba na tym znać. Jak mi jakaś część w furze nawali czy to wahacz czy przegub czy jeszcze co innego to delphie oe zawsze dobiore w normalnych pieniądzach.
haha już to widzę
nie znasz się, ale wypowiesz się