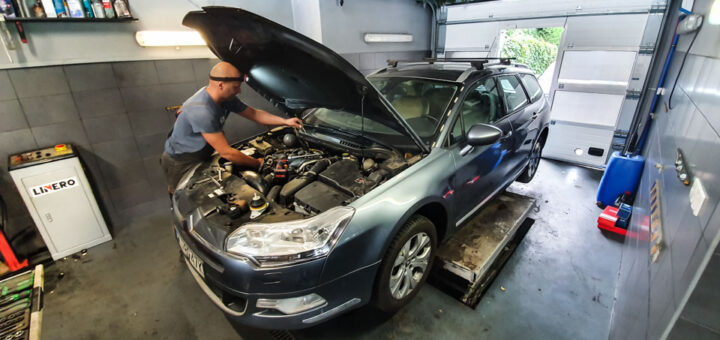
Preparaty ceramiczne dodawane do oleju, takie jak np. Ceramizator mają m.in. ograniczyć tarcie i wydłużyć trwałość silnika. Ma to zagwarantować warstwa ceramiczna powstająca w procesie ceramizacji silnika. Na czym polega ten proces, jak działa, jaką grubość ma powłoka ceramiczna i jak ona powstaje?
Proces ceramizacji w silniku jest dość interesującym zagadnieniem z zakresu tribologii (nauki o tarciu, zużyciu i smarowaniu) i tribochemii (reakcji chemicznych zachodzących pod wpływem tarcia). Proces ceramizacji polega na tworzeniu ochronnej warstwy ceramicznej na powierzchniach metalowych w miejscach, gdzie dochodzi do styku i tarcia, takich jak tłok, cylinder, wał korbowy i inne części silnika.
Na czym polega proces ceramizacji silnika?
Proces ceramizacji można opisać jako kontrolowaną reakcję chemiczną i fizyczną modyfikację powierzchni metalu, wywołaną poprzez dodatek ceramiczny w oleju silnikowym. W wyniku ceramizacji tworzy się cienka, ochronna warstwa, która charakteryzuje się wysoką twardością, odpornością na ścieranie i dużą wytrzymałością termiczną. Proces ceramizacji powłoki jest kilku etapowy, ale co ważne zachodzi tylko w obrębie tych elementów silnika, pomiędzy którymi ma miejsce intensywne tarcie generujące bardzo wysokie ciśnienie i temperaturę.
Zobacz: Płukanka do silnika – jak ją stosować?
Kolejnym elementem procesu jest dostarczenie aktywnych cząsteczek. Preparaty ceramiczne zawierają cząstki ceramiczne oparte na różnych związkach ceramicznych, takich jak dwusiarczek molibdenu (MoS₂), dwutlenek cyrkonu (ZrO₂), bor lub różne formy węgla (np. węgiel grafitowy lub diamentowy). Każdy z tych związków wykazuje skłonność do trwałego wiązania z metalami, tworząc twardą i wytrzymałą powłokę. W wysokiej temperaturze i pod wpływem tarcia dochodzi do chemisorpcji, czyli silnego wiązania chemicznego między powierzchnią metalu a aktywnymi cząsteczkami ceramicznymi. Aby chemisorpcja była możliwa, wymaga ona dostarczenia odpowiedniej energii aktywacyjnej, co umożliwia cząsteczkom ceramicznym przezwyciężenie sił odpychania elektronowego i zbliżenie się do powierzchni metalu na odległość umożliwiającą powstanie wiązań chemicznych. W silniku, energia ta jest generowana przez ciepło i siły tarcia.
Zobacz: Jak zmniejszyć zużycie oleju przez silnik? Najlepsze sposoby i metody
W miejscach największego tarcia i kontaktu metal-metal, powstają warunki sprzyjające reakcjom tribochemicznym – czyli zjawiskom chemicznym wywołanym mechaniczną energią tarcia. Cząsteczki ceramizatora, pod wpływem ciśnienia i wysokiej temperatury, ulegają trwałej adhezji do powierzchni metalu. W efekcie powstaje cienka, ochronna warstwa o twardości zbliżonej do ceramiki. Efektem procesu ceramizacji jest m.in. wypełnienie mikroskopijnych szczelin, rys i nierówności na powierzchni metalowych części. W wyniku tego powierzchnie chropowate stają się gładsze, co zmniejsza opory tarcia ślizgowego. Taka warstwa działa jak „samoregenerująca się powłoka” bo drobne uszkodzenia mogą być na bieżąco niwelowane dzięki dodatkom ceramicznym zawartym w oleju.
Charakterystyka powłoki ceramicznej i jej wpływ na tarcie
Powierzchnie metalowe tłoka i cylindra, a także inne ruchome części silnika, mogą na w punktach styku rozgrzewać się do temperatur sięgających nawet kilkuset stopni Celsjusza. Cząsteczki ceramiczne są zazwyczaj wykonane z materiałów o wysokiej stabilności termicznej, jak dwutlenek cyrkonu (ZrO₂) czy dwusiarczek molibdenu (MoS₂). W przypadku np. polskiego Ceramizatora jego bazowym składnikiem był z początku heksagonalny azotek boru (hBN), ale producent dość szybko udoskonalił formułę i oparł ją na minerale tworzącym dużo mocniejszą powłokę. Nie ulega ona degradacji ani rozkładowi w temperaturze do 400 stopni Celsjusza, wytrzymuje do 100 000 km i chroni elementy silnika przed ścieraniem i nadmiernym nagrzewaniem.
Powłoka ceramiczna ma niską adhezję, co oznacza, że zanieczyszczenia nie przylegają do niej tak łatwo jak do gołego metalu. Warstwa ceramiczna odpycha drobiny sadzy i inne zanieczyszczenia, ogranicza osadzanie się nagaru, przez co ruchome części mogą swobodniej pracować. Dodatkowo, taka powierzchnia jest również bardziej odporna na uszkodzenia spowodowane cząstkami stałymi, w tym opiłkami metalu, które mają właściwości szlifujące powierzchnie.
Zobacz: Dlaczego zapycha się odma silnika? Oto główne przyczyny
Kluczową rolą ceramizacji jest zmniejszenie współczynnika tarcia. Porowata struktura powierzchni metalowych generuje opory. Gładka, twarda warstwa ceramiczna ma niski współczynnik tarcia w porównaniu do powierzchni metalu-metal. Dzięki temu zmniejsza się tarcie ślizgowe i toczne, co ogranicza straty energii i opóźnia zużycie elementów. A im niższe straty mocy spowodowane tarciem, tym finalnie większa moc silnika jaka trafia na koła.
Jak gruba jest powłoka ceramiczna?
Powłoka musi być cienka, aby nie zakłócać precyzyjnych dopasowań między ruchomymi częściami silnika, takimi jak tłok i cylinder, które pracują w bardzo małych odstępach. Nadmiernie gruba warstwa mogłaby spowodować zbyt duże opory i prowadzić do zwiększenia zużycia paliwa lub nawet do uszkodzeń mechanicznych. Grubość powłoki ceramicznej, która tworzy się podczas ceramizacji w silnikach, jest zazwyczaj bardzo cienka i wynosi od kilku do kilkudziesięciu mikrometrów (μm). Standardowo jest to przedział około:
- 1-15 μm – dla warstw powstających w wyniku regularnej eksploatacji silnika z dodatkami ceramicznymi.
- do 30 μm – przy intensywniejszym stosowaniu preparatów ceramicznych lub po dłuższym czasie użytkowania.
Co ważne, tak cienka warstwa ceramiczna nie ma też negatywnego wpływu na honowanie cylindrów. Nie zakłóca jego działania, a wręcz ogranicza zużywania się struktury siatki honowniczej.
Efekty tribologiczne i korzyści wynikające z ceramizacji
Popularność dodatków ceramicznych do oleju rośnie z każdym rokiem, a trend ten i ich możliwości dostrzegli też producenci olejów silnikowych. Coraz więcej jest bowiem formulacji olejowych zawierających np. biały grafit. I choć nie działają one tak skutecznie jak typowe dodatki ceramiczne, to stanowią dowód na to, że ceramizacja silnika przynosi efekty. Te najważniejsze to:
- Zmniejszenie tarcia i zużycia: Ceramizacja zmniejsza współczynnik tarcia między częściami metalowymi, co bezpośrednio ogranicza ich zużycie. Dzięki temu elementy silnika mogą działać dłużej bez utraty swoich właściwości mechanicznych.
- Samoczynna regeneracja powierzchni: Powłoka ceramiczna w pewnym stopniu działa jako samonaprawiająca się warstwa ochronna. Mikrouszkodzenia, które powstają podczas pracy silnika, mogą być stopniowo uzupełniane przez cząstki ceramiczne z oleju.
- Zmniejszenie strat energii: Niższe tarcie oznacza mniej energii traconej na pokonanie oporu mechanicznego, co przekłada się na większą sprawność silnika. Choć wzrost mocy wyjściowej jest zazwyczaj niewielki, to przy intensywnej eksploatacji różnice mogą być zauważalne. Mniejsze straty, to większa moc na kołach.
- Ochrona przed korozją i oksydacją: Powłoka ceramiczna chroni metalowe powierzchnie przed utlenianiem, co jest istotne zwłaszcza w starszych silnikach i podczas ich długotrwałej eksploatacji.
Czy ceramizacja rzeczywiście działa?
Proces ceramizacji, oparty na zasadach tribologicznych i tribochemicznych, ma realne podstawy naukowe. Dobrze przeprowadzona ceramizacja może przynieść korzyści w postaci zmniejszenia tarcia i poprawy trwałości elementów silnika. W praktyce, efekty te są bardziej zauważalne w silnikach starszych i wyeksploatowanych. W nowych silnikach, które są zaprojektowane z wysoką precyzją i wąskimi tolerancjami, różnice mogą być mniejsze, ale proces nadal może chronić przed mikrouszkodzeniami i zwiększyć żywotność jednostki napędowej. Jest to szczególnie istotne w przypadku nowoczesnych silników małolitrażowych z turbodoładowaniem, które z jednej strony mają wysoki stopień wysilenia, a z drugiej coraz mniejsze przekroje części. A same podzespoły, z racji ekologii, ograniczania masy, norm WLTP i oszczędności na etapie produkcyjnym, nie są obecnie tak mocno utwardzane, jak te 20-30 lat temu.
Zobacz: Dlaczego silnik bierze olej? Oto główne przyczyny
Dodaj komentarz