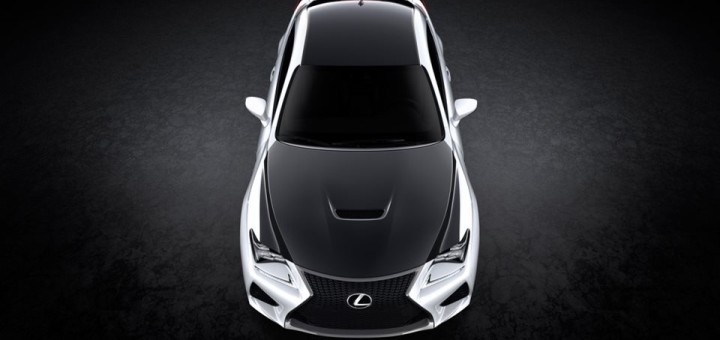
Carbon, czyli kompozyty zbrojone włóknem węgłowym, używany jest w motoryzacji do produkcji m.in. nadwozi sportowych samochodów. Coraz częściej wykorzystywany jest on także jako budulec takich podzespołów jak wał napędowy czy sprężyny amortyzatorów. Jak powstaje carbon?
Kompozyty zbrojone włóknem węglowym, czyli Carbon Fiber Reinforced Plastics (CFRP) – bo tak brzmi prawidłowa nazwa materiałów określanych skrótowo słowem carbon – to materiały stworzone z myślą o przemyśle lotniczym i kosmicznym. Ich podstawową zaletą jest wielka wytrzymałość przy małej masie. Włókno węglowe ma wytrzymałość na rozciąganie ponad czterokrotnie większą od najlepszej stali, jest jednak bardzo giętkie, więc dla zapewnienia wymaganej sztywności łączy się je z twardymi żywicami syntetycznymi, na przykład epoksydowymi. Włókna węglowe, a właściwie wykonana z nich wielowarstwowa tkanina, pełnią wówczas rolę zbrojenia, a spajająca je żywica nadaje kompozytowym elementom pożądany, trwały kształt.
Zobacz: Jak wygląda kierownica wyścigowego bolidu?
Elementy kompozytowe wykonuje się w foremnikach, stanowiących negatyw kształtu wytwarzanego przedmiotu, z użyciem jednego z kilku podstawowych sposobów. Najprostszy to laminowanie, polegające na układaniu kolejnych warstw tkaniny (węglowej, kevlarowej, szklanej itp.) i ręcznym przesycaniu ich żywicą zmieszaną z utwardzaczem. Wadą tej metody jest ograniczenie czasem twardnienia żywicy, powodujące pośpiech sprzyjający błędom wykonania.
Zobacz: Honda stworzyła silnik o zmiennej pojemności skokowej!
Drugi sposób to wykorzystanie tzw. prepregów (preimpregnatów), czyli wielu warstw tkaniny wstępnie przesyconych żywicą. Trzecia metoda, zwana RTM (Resin Transfer Molding) polega na ciśnieniowym wypełnianiu żywicą foremnika zwierającego uprzednio ułożoną tkaninę. I wreszcie czwarty sposób, C-SMC (Carbon Fiber Reinforced Sheet Molding Compound), to wtryskiwanie żywicy zmieszanej z drobno pociętymi włóknami do formy – prostota i szybkość tej ostatniej jest okupiona niższą wytrzymałością wykonanych z jej użyciem elementów. Dla ostatecznego utwardzenia żywicy elementy wymagają kilku godzin wygrzewania w temperaturze rzędu 180 stopni Celsjusza. Końcowy etap obróbki to szlifowanie krawędzi, wiercenie otworów montażowych itd.
Zobacz: Zawory wypełnione sodem – jakie są ich zalety i wady
Modelem, w którym na największą skalę zastosowano kompozyty węglowe, był sportowy supersamochód Lexus LFA, w którym z materiałów tych wykonano aż 65 procent struktury nadwozia. W ten sposób udało się uzyskać masę pojazdu o 100 kg mniejszą, niż w przypadku konwencjonalnej struktury metalowej. Główną ramę kabiny wytworzono korzystając z prepregów, tunel wału napędowego, panele podłogi, dach i pokrywę silnika wykonano metodą RTM, a tylne słupki i tylną część podłogi – metodą C-SMC.
Warto zauważyć, że w przeciwieństwie do innych producentów Lexus zdecydował się wdrożyć całość procesu produkcyjnego kompozytów węglowych we własnym zakładzie, budując nawet własną, zautomatyzowaną linią wytwarzania tkanin węglowych. Opracowano również oryginalną technologię łączenia kompozytów z aluminiowymi okuciami mocowania silnika i zawieszenia.
Zobacz: Jak działa turbosprężarka ze zmienną geometrią kierownicy VGT?
Doświadczenia zgromadzone podczas produkcji modelu LFA zaprocentowały przy wdrażaniu kolejnych modeli, pozwalając ograniczyć masę elementów położonych powyżej środka ciężkości pojazdu, co korzystnie wpływa na jego stabilność. Dziś wykonany z kompozytów węglowych dach, maskę i spojler możemy zobaczyć np. w sportowym Lexusie RC F Carbon.
Zobacz: Lexus LC 500 – najciekawsze fakty i dane
Źródło: materiały prasowe Lexus
Dodaj komentarz